The Problem: Heat vs. Size
When camera engineers attempt to shrink a body while increasing its power (think 8K RAW, 120fps, ProRes), things get hot. Traditional heat sinks and fans take up space. Stacking heat-producing components like the sensor, processor, and cooling unit on top of one another creates bulky bodies—the antithesis of sleek, modern design. In many mirrorless or cinema-style bodies, cooling solutions feel like an afterthought—resulting in workarounds like dummy batteries, external fans, or even firmware-limited record times. Canon EOS R5 8K RAW Shooting Overheating Issue Solved shows just how persistent this issue has been.
The Invention: A Smart, Spread-Out Cooling System
This patent offers a refreshingly clean approach: place the sensor board (imaging substrate), the main processor board (control substrate), and the active cooling unit side-by-side along the camera’s optical axis direction (i.e., depth-wise), instead of stacking them.
Here’s what makes it work:
- Inline Layout: By placing each heat-sensitive part linearly (instead of vertically), you save on depth while still allowing airflow to hit each target.
- Ducted Fan Cooling: A fan blows air through a duct connected to both the sensor and processor. That duct is smartly shaped to fit within the camera’s tight frame.
- Dual Heat Paths: In case the fan fails or is off, a graphite heat sheet channels residual heat to the metal chassis for passive dissipation.
- Signal Isolation: Signal lines and cooling elements are physically separated to prevent electrical interference or image degradation—a common issue in high-speed imaging.
Deep Dive: Breaking Down the Patent Architecture
The internal arrangement proposed in US 20250126335 A1 is deceptively elegant and highly functional. Canon’s engineers are clearly addressing long-standing pain points with heat buildup in compact bodies—not by merely slapping on external fans or expanding heat sinks, but by rethinking how heat moves within the camera. The patent reveals a holistic redesign, balancing thermodynamics with tight spatial constraints. Here’s a deeper look at its critical components and how they work together:
The internal arrangement proposed in US 20250126335 A1 is deceptively elegant. Let’s look at its architecture through a more detailed lens:
- Component Alignment in the Z-Direction:
- The image sensor, processing board, and cooling unit are aligned in the Z-axis (depth direction). This avoids unnecessary stacking and allows a more planar chassis profile.
- Airflow Duct Engineering:
- The patent describes a strategically routed fan duct (201a in diagrams) that directs airflow over the heat sources. The duct is designed to minimize dead air zones and optimize cooling without external bulk.
- Heat Transfer Layers:
- Graphite sheet 1 connects the sensor substrate to the duct. Graphite sheet 2 connects the sensor to the metal chassis. This ensures a secondary passive path for heat, even if airflow is interrupted.
- Cooling Unit Integration:
- Unlike external fans or accessories, this unit is integrated as a core part of the design. It’s thermally coupled yet modular—suggesting easy maintenance and potential silent operation.
- Sensor Stability Considerations:
- The design ensures that heat buildup near the sensor does not affect imaging performance—particularly important for long RAW takes or low-light exposures.
- Venting Location:
- The side of the camera (202a) features discreet but efficient air vents that allow hot air to exit the system without interfering with operator handling or accessory mounts.
Each of these design elements contributes to a unified goal: compact, quiet, and consistent performance in demanding environments. Moreover, the modular nature of the cooling system means that different tiers of the same camera model could scale up or down based on heat dissipation requirements—allowing for product line flexibility across consumer, prosumer, and cinema-grade devices. Another standout feature is the redundancy built into the system. The dual-path approach ensures that even if one cooling method is compromised (e.g., fan failure or blocked vent), the graphite-based passive cooling continues to pull heat away from the sensor and main board. This kind of fail-safe thinking is rare in consumer electronics, yet essential for professional-grade reliability. Also worth noting is the patent’s emphasis on electrical isolation. Heat-generating components and signal lines often interfere with one another, causing noise or artifacts in the image. By physically distancing and thermally decoupling them, Canon’s design improves both operational stability and image purity—an understated but vital advantage for high-ISO, high-bitrate shooters. Taken together, this isn’t just thermal engineering; it’s a blueprint for the next generation of compact cinema cameras. Whether Canon integrates this into a successor to the EOS R5C or a new dedicated cinema body remains to be seen—but the potential is unmistakable.
Why This Matters for Small Cameras
This design enables a flatter, more compact layout of key components while maintaining effective heat management. The upshot?
- Smaller body sizes for cameras that can still handle 8K and high-frame-rate capture.
- More efficient passive and active cooling, making shutdowns during long takes less likely.
- Reduced noise from better airflow management and isolation.
- Fewer compromises in ergonomics, battery life, or recording formats.
For mirrorless bodies that double as cinema tools—like the Sony FX3 or Canon R5C—this could be a game-changer. Imagine a future Sony A9-sized 8K RAW beast that stays cool without a cage and fan. Nikon Z8 Never Overheats When Shooting 8K Compressed RAW proves it’s possible—if the internal design is smart enough.
The Materials: Graphite Sheets and Heat Pipes
The patent isn’t just about placement; it’s also about what you build with. The system uses:
- Graphite sheets: These transfer heat laterally from the sensor and processor to both the fan duct and the chassis.
- Heat pipes: For sections where heat needs to jump components or move around corners.
- Thermal resistance management: By adjusting the thermal properties of each material, heat can be routed more efficiently and predictably.
This aligns with recent filings such as Canon Patents an Enhanced Heat Dissipation Solution and Panasonic Patents a Heat Dissipation Mechanism for a Compact Cinema Camera, signaling an industry-wide shift toward smarter, smaller thermals. It’s mechanical engineering that reads like choreography.
More Than Just a Cool Idea
What’s truly exciting about this patent is that it isn’t just for show. It represents a practical, implementable improvement to the internal architecture of cameras.
If this design is adopted, expect:
- Longer record times without overheating
- Fanless silent operation in low-power modes
- True run-and-gun 8K shooting without bulk and even in an ultra-compact structure.
It might even inspire new product categories: compact cine cams, hybrid vlog rigs, or even AI-onboard smart cameras that won’t cook themselves alive.
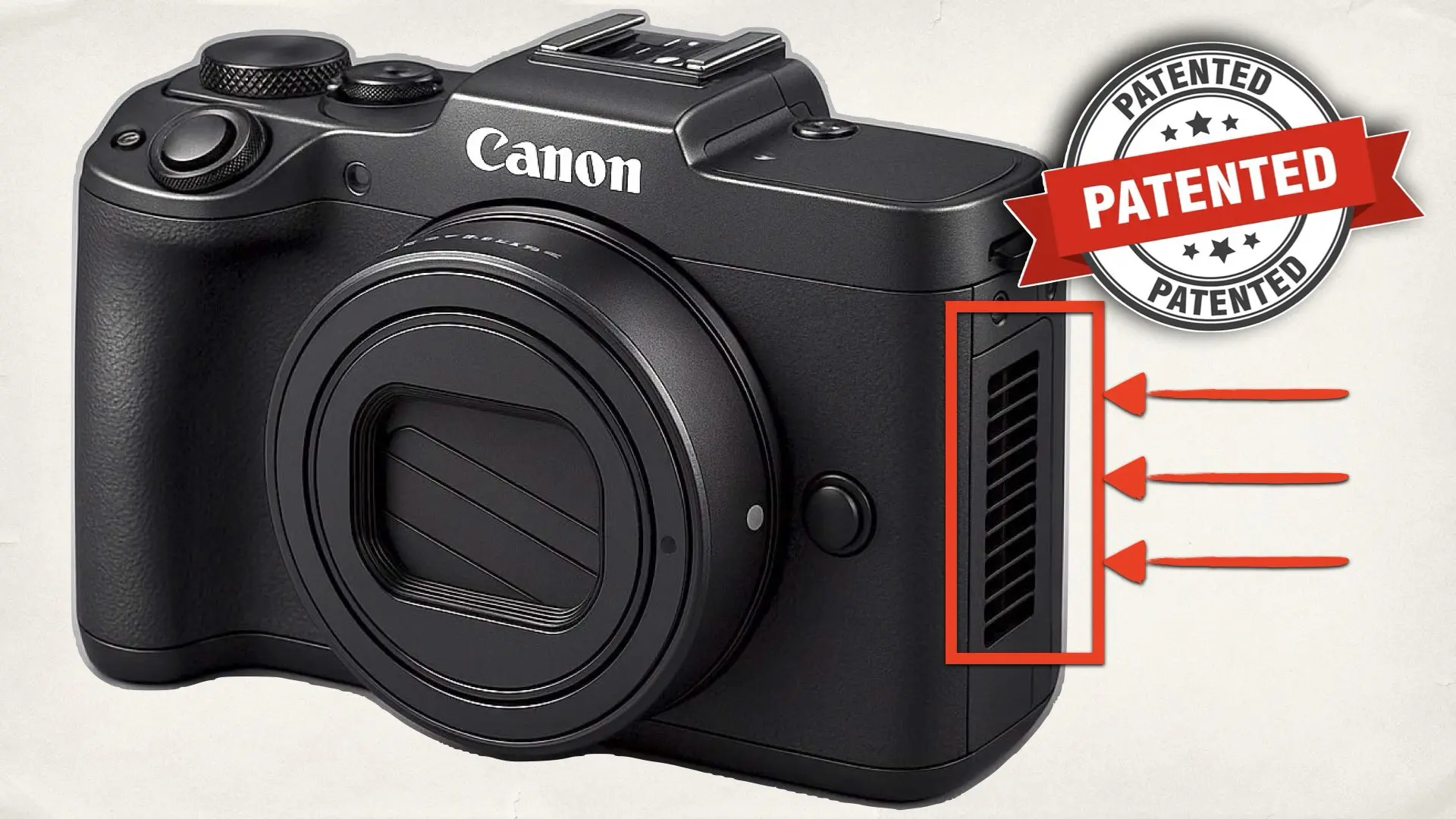
Final Frame
Patent US 20250126335 A1 is a fine example of form and function intersecting in camera design. It doesn’t reinvent heat dissipation—it refines it with surgical precision for modern use cases. The real win? It lets camera manufacturers scale down the body while scaling up the power. And for creators, that means shooting longer, sharper, and cooler—literally.